What Is Preventative Maintenance and Why Do You Need It?
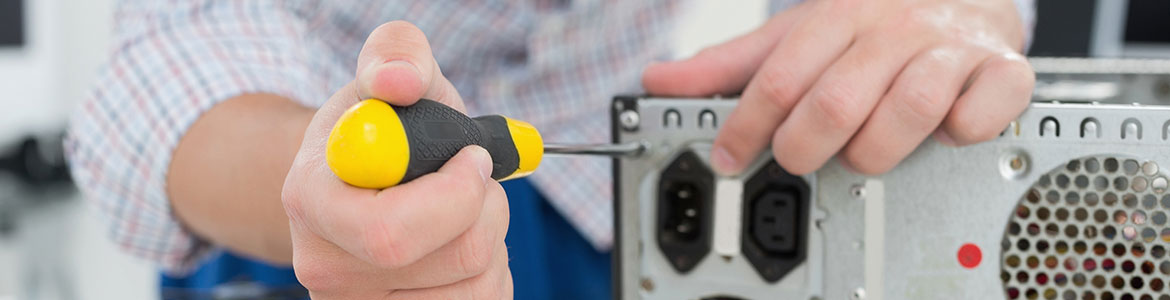
You're used to thinking about maintenance as something that happens when your equipment breaks. You don't have time to think about it before or after your equipment is fixed.
If you're spending a lot of money on emergency maintenance, or your workload is disrupted because a piece of equipment has suddenly stopped working, your company needs to implement preventative maintenance.
Preventative maintenance is the term used to describe regular maintenance performed with the intention to keep machinery and equipment running smoothly. The practice uses a schedule to keep valuable assets working and make sure downtime is reduced, or even eliminated when possible.
For example, an office that relies on central heating to keep the building warm in the winter would perform maintenance on each heating unit in September, shortly before the cool fall weather settles in. Instead of waiting for when the heating breaks, preventative practices ensure the unit keeps working at top performance by performing tune ups and part replacement ahead of time.
When a piece of equipment breaks unexpectedly, you need it to become functional as soon as possible. This often results in costly emergency repairs because of the necessary rush. Unplanned maintenance often costs three to six times more than planned maintenance because of the speed needed to fix broken assets.
When you can count on your equipment continuing to work, you and your employees will be safer in your work place. Unmaintained machines pose a serious threat to the health and safety of your workers. Depending on the type of equipment you use, machinery breaking while in use can lead to serious accidents. Not only will you have to pay the costs of repairing your equipment, but you'll likely have to pay for worker's compensation. Depending on the severity of the accident, you also risk going to court to address the damage done to your employees.
You can avoid all of this by taking the time to maintain your assets before they are in danger of breaking. Your workers will be happy and safe, and your company won't have to worry about damage control.
Preventative maintenance is more difficult to carry out than waiting for equipment to break, because managers need to create a maintenance schedule for company assets. Some companies rely on mechanics to inform them about their asset needs and behaviors they can expect to see. Others rely on paper records to inform them of previous issues.
With the help of asset tracking and maintenance planning software, planning your maintenance needs can become less complicated. You won't need to rely on mechanics who might not be familiar with your specific asset, or old and outdated paper records. Asset Panda's flexible platform is designed specifically to help you create an efficient maintenance schedule for all of your assets.
Our cloud-based software allows employees in all parts of your company to update your asset database. Having recent information about your equipment allows you to make informed decisions about when to send in your assets for repairs.
Regularly-updated asset information also allows you to see asset use over time. Gathering information over time allows you to see peak usage hours, and times when specific assets are less likely to be used. These records make it easy for you to schedule asset maintenance during the least disruptive time.
Want to see how Asset Panda can help you schedule preventative maintenance? Sign up for a free trial today!
If you're spending a lot of money on emergency maintenance, or your workload is disrupted because a piece of equipment has suddenly stopped working, your company needs to implement preventative maintenance.
What Is Preventative Maintenance?
Preventative maintenance is the term used to describe regular maintenance performed with the intention to keep machinery and equipment running smoothly. The practice uses a schedule to keep valuable assets working and make sure downtime is reduced, or even eliminated when possible.
For example, an office that relies on central heating to keep the building warm in the winter would perform maintenance on each heating unit in September, shortly before the cool fall weather settles in. Instead of waiting for when the heating breaks, preventative practices ensure the unit keeps working at top performance by performing tune ups and part replacement ahead of time.
How Can Preventative Maintenance Help You?
When a piece of equipment breaks unexpectedly, you need it to become functional as soon as possible. This often results in costly emergency repairs because of the necessary rush. Unplanned maintenance often costs three to six times more than planned maintenance because of the speed needed to fix broken assets.
When you can count on your equipment continuing to work, you and your employees will be safer in your work place. Unmaintained machines pose a serious threat to the health and safety of your workers. Depending on the type of equipment you use, machinery breaking while in use can lead to serious accidents. Not only will you have to pay the costs of repairing your equipment, but you'll likely have to pay for worker's compensation. Depending on the severity of the accident, you also risk going to court to address the damage done to your employees.
You can avoid all of this by taking the time to maintain your assets before they are in danger of breaking. Your workers will be happy and safe, and your company won't have to worry about damage control.
Preventative maintenance is more difficult to carry out than waiting for equipment to break, because managers need to create a maintenance schedule for company assets. Some companies rely on mechanics to inform them about their asset needs and behaviors they can expect to see. Others rely on paper records to inform them of previous issues.
With the help of asset tracking and maintenance planning software, planning your maintenance needs can become less complicated. You won't need to rely on mechanics who might not be familiar with your specific asset, or old and outdated paper records. Asset Panda's flexible platform is designed specifically to help you create an efficient maintenance schedule for all of your assets.
Our cloud-based software allows employees in all parts of your company to update your asset database. Having recent information about your equipment allows you to make informed decisions about when to send in your assets for repairs.
Regularly-updated asset information also allows you to see asset use over time. Gathering information over time allows you to see peak usage hours, and times when specific assets are less likely to be used. These records make it easy for you to schedule asset maintenance during the least disruptive time.
Want to see how Asset Panda can help you schedule preventative maintenance? Sign up for a free trial today!
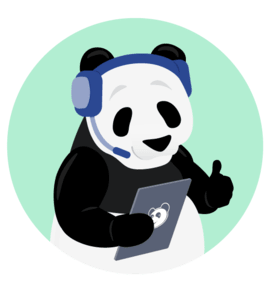
Learn more from an Asset Panda expert
Get a FREE consultation with an asset tracking expert to find out how you can transform your asset tracking.
Contact our Sales Team at (888) 928-6112