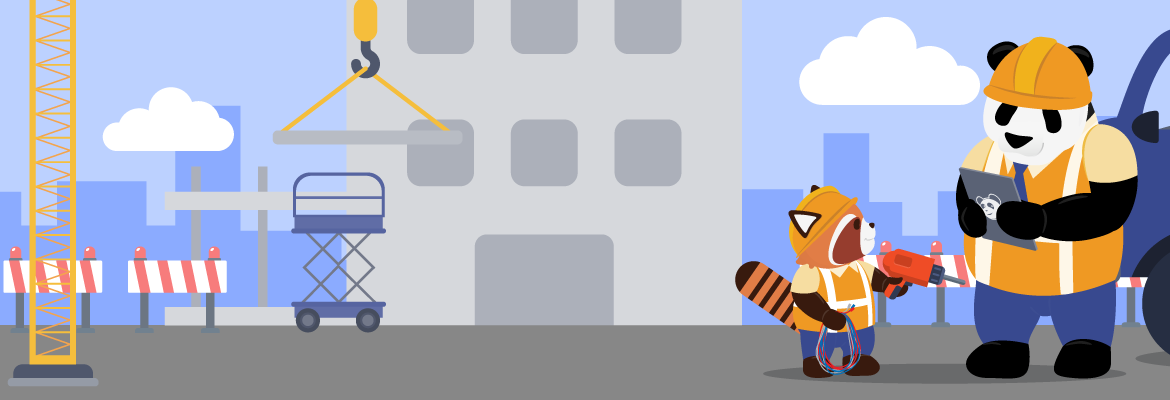
Electrical Construction Company
Saves Several Hours of Work
per Day with Asset Panda
Summary
As one of the most prolific electrical construction contractors on the West Coast, this company has extensive experience across all industry groups and delivery models, including tech office spaces, historical renovations, high-rise commercial and residential towers, and industrial and manufacturing process facilities.
Between its two locations, the company currently manages upwards of 40,000 assets. These assets span two main categories: construction tools and IT devices. With such a large number of assets over various categories, their team was spending lots of valuable time simply trying to keep track of everything.
The Challenge
Before signing on with Asset Panda, the electrical construction company struggled with tedious and manual asset management methods. The biggest challenges they faced include:
- Tool tracking: Prior to using Asset Panda, the team would rely on manual workflows to get their tools to and from job sites. When a Field Manager wanted to return items to the warehouse from a job site, they would handwrite the tool numbers, then give those tools and the list of numbers to the driver and send them on their way. The driver did not have their own additional step to confirm the items loaded onto the truck, which often led to discrepancies between the report and the tools being returned. This handwritten reporting process not only took quite a bit of time, but also made it difficult for managers to properly track tool fade.
- Tool fade: Without a single source of truth for their tool data, the company knew they were experiencing tool fade, but didn't know exactly what was happening to these items. At the end of a job, the team would decide which unaccounted-for items needed to be replaced and reorder them accordingly. With an average tool price in the $20,000-50,000 range, replacing these items came at a high cost.
- Auditing: The company's original auditing method proved very time-consuming for their team before Asset Panda. Previously, they would print a report of the tools needed for the job that day, then handwrite the names of items or take pictures of their barcodes, all of which would typically take an entire day's work for 2-3 people. But, without a way to aggregate this data and create audit trails, they were not able to find any data trends from these audits or pinpoint the source of the problem. "Before Asset Panda, we didn't have any data," the Implementation Specialist says.
The Solution
The electrical construction company first signed on with Asset Panda in 2017 to manage their California warehouse. Their Implementation Specialist cites Asset Panda's customization as one of the main reasons for their decision. "We could really build it out the way we wanted it to be built out."
After quickly realizing the benefits, they scaled their program in 2018 to track assets in their Seattle location as well. While the team initially used Asset Panda to track the construction tools going in and out of the warehouses, they soon began tracking their IT devices as well.
After getting on board, the company's main goal was to set up better tracking processes so they could have accurate data, less tool fade, and better accountability. Rather than manually writing down the tools going to and from job sites, their team now has a multi-step process in place for tool returns.
- Using the Asset Panda mobile app, the Field Manager does a group scan of the items they want to return and conducts an action which sends a transaction report to the local warehouse.
- After receiving the transaction report, the warehouse then dispatches a driver to retrieve the items from the job site.
- Once at the job site, the driver then checks the assets against the transaction report to confirm the items before heading back to the warehouse.
- Back at the warehouse, the driver completes the tool return, and another transaction report is generated and shared with the General Foreman of the job site.
- The Warehouse Manager then looks at the report and what was actually returned to reconcile any discrepancies.
While tracking tools to and from job sites has certainly helped the team cut tool fade, refining their auditing process has been another key factor. With their previous manual audit methods, the team would know they were missing tools but couldn't say exactly when or where they went missing – especially on 2–3-year jobs. The company wanted to make it easy for their Field Managers to request an audit, so they created an Audit Request Form. Once that form is received, Administrators or Warehouse Managers will create and assign the audit to the Field Manager to conduct through the Asset Panda mobile app. "Now, we have no other way to get [our transactions] done," the Implementation Specialist says.
The Results
By using Asset Panda to track all their construction tools and IT devices, the electrical construction company saves "several hours [a] day" of manual work and has accurate data to inform their business decisions.
Number of Assets Tracked: 43,000+
Transactions per Day: 100+
Reports Created: 121 group reports, 924 action reports, 27 change reports, 22 audit reports
Asset Panda Admins Onboarded: 15-20
Conclusion
Over the past 5+ years, this electrical construction company has used Asset Panda to its fullest extent to streamline tool requests and audits and reduce tool fade. Aligned with their value of continuous improvement, the team plans to work alongside the Asset Panda team to further customize and scale their program.
"As a team, we're constantly putting our heads together and saying, 'What are we doing now and how can we do it better?'" the Implementation Specialist says. "The flexibility of what we can do in Asset Panda makes it attainable for us to push the software even further."
"Using Asset Panda for tool requests or checkouts has saved several hours a day of somebody's work."