A Quick Guide to Kitting Automotive Tools

Take Control of Your Assets
A personalized demo is just one click away.
You and your team at your mechanic shop use dozens of tools to work on client vehicles. You might have a good solution for storing your tools or you might be struggling with what to do about your tool storage. Have you thought about kitting some of your tools together? Kitting can help you track tools without having to track every single piece. Since you use dozens of tools, trying to track them all at once can be overwhelming.
Today’s article will define kitting, and how you can apply it to your automotive shop.
What is Kitting?
Kitting is the process of packaging and storing items together. When you kit items together, you combine related items for easier usage. Often times, this refers to packaging goods and selling them as a kit. However, the term often is used for keeping related tools together.
Kitting can refer to what you have in your toolbox. So if you already have a toolbox or tool storage solution, you’re already using kitting solutions!
How to Kit Automotive Tools Together
There are several steps to kitting automotive tools. The first one is knowing what tools you have on hand. Record everything, even the things you don’t use or didn’t know you had.
Once you know what you have, document where each of those tools is located in your shop. Where do you tend to use them? Do some tools travel around? Do others tend to stay where they are because of size? What do you tend to use in the shop, and what sometimes travels outside of it?
These are all good starting points for kitting your tools together.
The next step is identifying the assets you tend to use together. Wrenches, screwdrivers, and small tools often get used at the same time.
Another part of the process is to identify your storage capacities. What can you store separately, and what can get packaged together to save on space?
Document Kitting Procedures
Once you’ve identified all of these points, you’ll need to document kitting procedures. What are you storing in each toolbox? What pieces should be present, and which should be stored separately?
Another thing you’ll need to track is who is allowed access to different kits? Does each mechanic have their own set, or does everyone have to share? Depending on what model you decide to use, you may need to implement check-in and check-out procedures. Implementing these procedures helps you track where your kits are located, who used them last, and can help you track down individual items that may have gone missing.
Creating a system where you can track these kits is an important aspect of the kitting process. Asset Panda is designed to become the type of asset tracking program you need. With cloud storage capacities, you can update kits on one end of your car bay, and the manager in the office will see it within seconds. Then, the manager can figure out what else is needed and what other kitting procedures need to happen. Asset Panda will also help you track vehicle repairs, and you can connect the kits to which vehicles they were used on, creating a holistic business tracking solution you can use in all aspects of your mechanic business.
Take Control of Your Assets
A personalized demo is just one click away.
Related News & Press
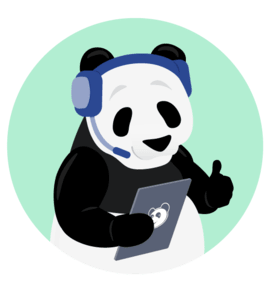
Learn more from an Asset Panda expert
Get a FREE consultation with an asset tracking expert to find out how you can transform your asset tracking.
Contact our Sales Team at (888) 928-6112