Get real-time visibility into your equipment
Easily track and manage your equipment on the web or on mobile
Monitor the status, location, and condition of your assets with our real-time equipment management software. Ensure your tools and equipment remain in working order and assign available equipment to workers for enhanced accountability.
Plus, empower your team to check out equipment or request repairs from anywhere with our mobile app with available offline mode. Generate and print your own unique barcodes or QR codes and scan them directly on your mobile device – no third-party scanners required.
Stay ahead of maintenance
Create and assign work orders in one easy-to-use system
Streamline preventive maintenance and work orders with our comprehensive equipment maintenance software. With visibility into your equipment’s full repair history, key maintenance dates, and overall utilization, you can accurately forecast and schedule upcoming maintenance tasks.
Create custom work orders and assign them to available team members to increase productivity and prevent bottlenecks. With our centralized equipment management software, you can effectively manage workloads and reduce potential downtime.
Track the full lifecycle of your equipment
Optimize equipment utilization and reduce costs
Access the entire lifecycle history of your equipment from acquisition to disposal with our robust equipment maintenance software. Track every update in our detailed asset records, including assignment and repair history, recommended maintenance dates, and current depreciated value. By giving you full insight into an item’s current condition and value, our equipment management software helps you optimize asset utilization and improve cost savings.
Make better data-driven decisions
Increase productivity and uptime with custom alerts and reports
Gain the actionable insights you need to keep your team productive with real-time notifications and automated reports. With our equipment maintenance software, you can create custom notifications to alert you of work order requests, status changes, and more to maximize efficiency. Generate reports with virtually unlimited filters and create automated reporting schedules so you can easily monitor the state of your equipment, work order statuses, and more.
With detailed insights into your equipment, our equipment management software can help you optimize utilization, determine when assets need to be retired, and estimate costs for future purchases.

Unlimited Users
Get your entire team on the same page and set custom user permissions.

Streamlined Work Orders
Easily create and assign work orders for increased efficiency.

Customizable Workflows
Configure the platform to match the way you already work.
Useful features for equipment management
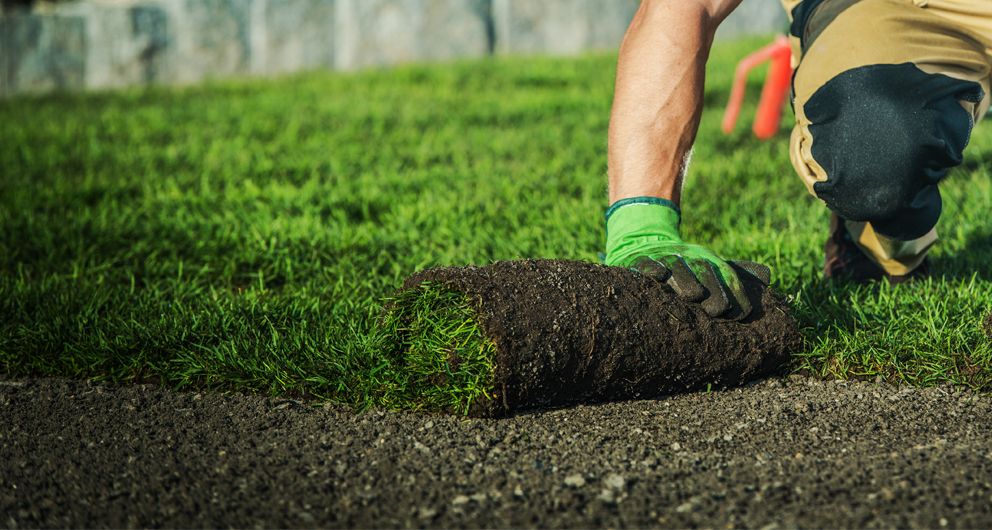
The Budd Group gives employees easy access to vehicle info
“Depending on their level of access, employees and managers can find everything they need about a vehicle in one place, from training to a location to a vehicle inspection history and maintenance needs.”
Dale Christensen
Operations Manager
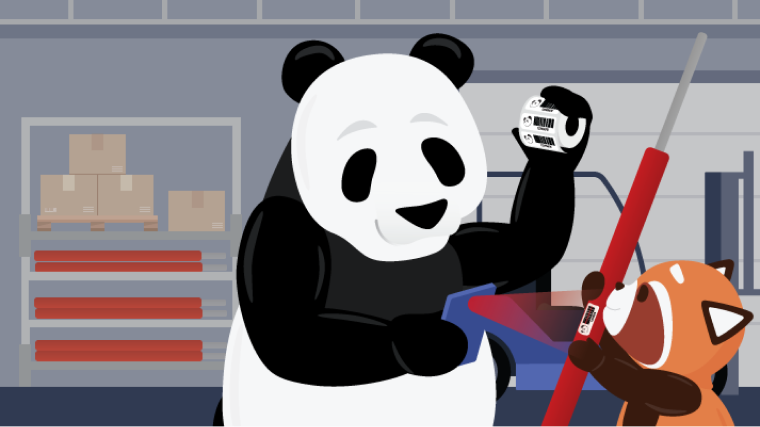
RISE™Robotics Uses Asset Panda as Their Single Source of Truth
"Almost every company that I could see myself working for in the future would benefit from something like Asset Panda if they don't already have it."
Tom Rufo
Lab Manager
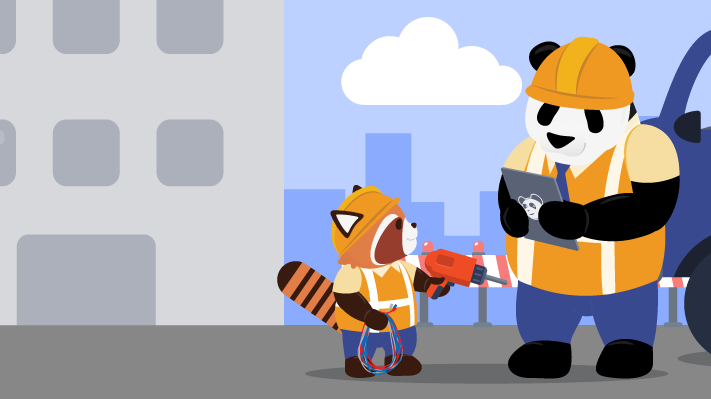
Electrical Construction Company Saves Several Hours of Work per Day with Asset Panda
"As a team, we're constantly putting our heads together and saying, 'What are we doing now and how can we do it better? The flexibility of what we can do in Asset Panda makes it attainable for us to push the software even further."
Implementation Specialist
Related equipment resources
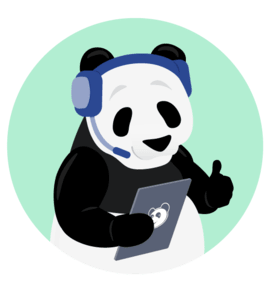
Learn more from an Asset Panda expert
Get a FREE consultation with an asset tracking expert to find out how you can transform your asset tracking.
Contact our Sales Team at (888) 928-6112