Easily manage maintenance schedules
Create work orders and assign them to available technicians for increased efficiency
Monitor and schedule preventive maintenance tasks and work orders in our computerized maintenance management system. Create and assign work orders to available team members to stay on track and prevent bottlenecks. Easily attach the right asset to your work order for increased efficiency in our centralized CMMS software.
With full visibility into your workforce, tools and equipment, and parts inventory, you can effectively manage workloads for maximum productivity.
Reduce costs and downtime
Make more informed decisions with real-time CMMS monitoring and notifications
Gain the actionable insights you need to keep your team productive with real-time notifications and automated reports. With our computerized maintenance management system, you can create custom notifications to alert you of work order requests and low inventory levels to maximize efficiency and uptime. Generate reports with virtually unlimited filters and create automated reporting schedules so you can easily monitor work orders, your parts inventory and equipment, and more.
Boost efficiency with barcode scanning
Save time and reduce manual effort with our mobile app with built-in barcode technology
Empower your employees to conduct workflows from anywhere (even when offline) using our mobile app with built-in barcode technology. Generate and print your own barcodes or QR codes directly in Asset Panda and scan them with your mobile device – no third-party scanners required. With our mobile CMMS software, your team can seamlessly complete work orders or inspections, all while saving time and improving data accuracy.
Improve accountability and compliance
Manage your employees' progress and enhance compliance in our centralized CMMS software
Add your entire team to our computerized maintenance management system with unlimited users, and grant the right access to the right people with customizable roles and permissions. House important safety and user manuals in your asset records and keep track of each employee’s training progress to increase compliance. Plus, enforce your standardized processes with signature capture and required notes or photos to boost accountability after each maintenance task.

Unlimited Users
Get your entire team on the same page and set custom user permissions.

Streamlined Work Orders
Easily create and assign work orders for increased efficiency.

Customizable Workflows
Configure the platform to match the way you already work.
Useful features for maintenance management
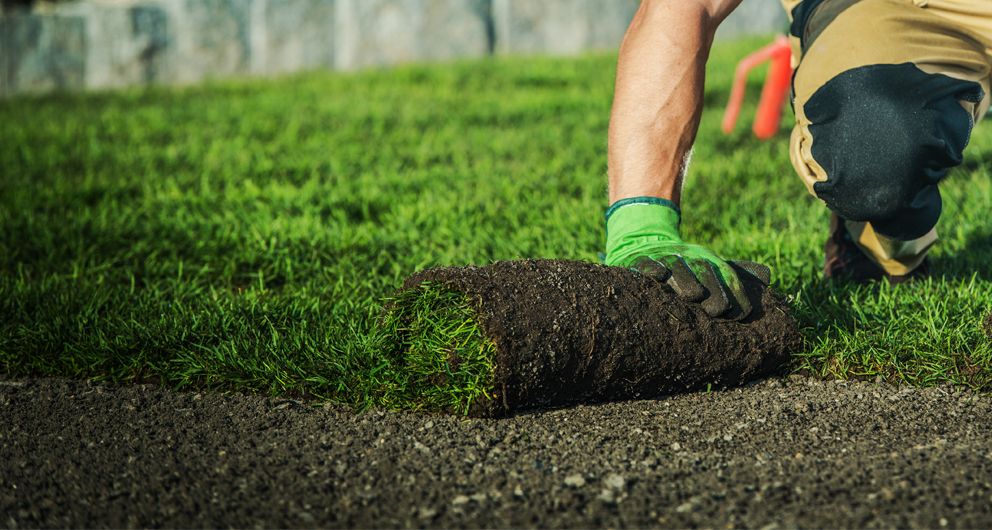
The Budd Group gives employees easy access to vehicle info
“Depending on their level of access, employees and managers can find everything they need about a vehicle in one place, from training to a location to a vehicle inspection history and maintenance needs.”
Dale Christensen
Operations Manager
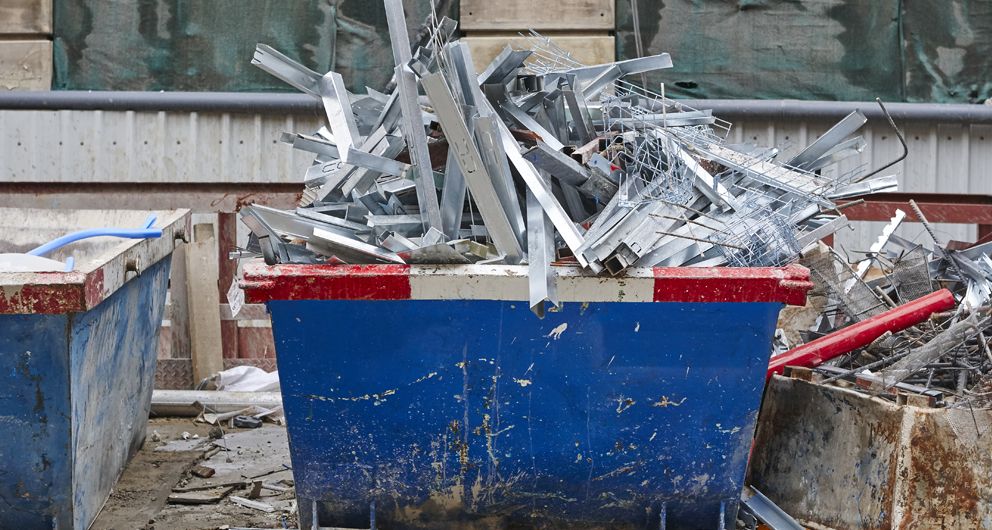
Waste Initiatives recovers two hours a day in previously lost spreadsheet time
“I’d say we’ve recovered two hours a day with Asset Panda. Previously, we spent those two hours fighting against our spreadsheet system, trying to track down equipment, figure out whether it was time to service something...Now, these are all things that happen automatically...”
Dwayne Smith
Director
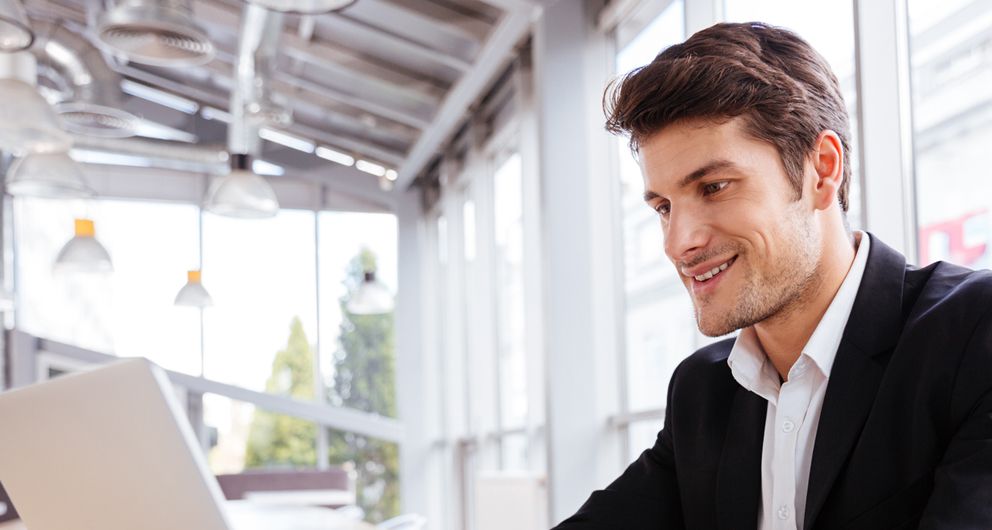
Allied Protection Services, Inc. has maintenance records at their fingertips
“I recently had what I’d call a “true Asset Panda moment.” The CEO asked for a report regarding our company vehicles. Thanks to Asset Panda, I was able to compile the report with the necessary data (which was up-to-date and in real time), print it and present it in less than five minutes!”
Daryl Jackson
Asset & Materials Coordinator
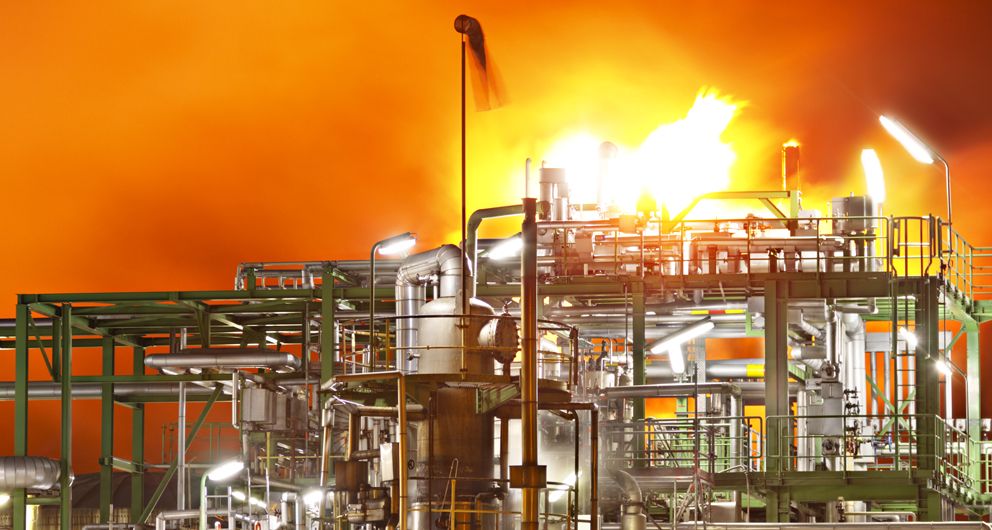
Covenant Testing Technologies ditches Excel forever
“It was hard to keep up with repairs and everything via Excel. We quickly discovered that Excel isn't “live” -- so we had to send the Excel spreadsheet to all employees so they could view asset data, that may not even be up-to-date.”
Johnathan Miller
Operations Coordinator
Related maintenance resources
Frequently asked questions
What is a CMMS?
CMMS stands for computerized maintenance management system. CMMS software is designed to help organizations manage work orders and track assets (e.g., parts inventory, tools and equipment) for increased efficiency and compliance.
What are the benefits of CMMS software?
CMMS software helps organizations to:
- Streamline work order management and scheduling
- Gain visibility into their parts inventory levels and the availability of tools and equipment
- Increase workplace safety and regulatory compliance
- Reduce potential downtime with real-time monitoring and notifications
- Save time with barcode scanning and automated processes
Who uses CMMS software?
A CMMS is useful for numerous organizations looking to manage their work orders, team members, and assets in one cohesive place. Industries that commonly use CMMS software include:
- Manufacturing
- Facilities management
- Transportation and logistics
- Hospitality
- Energy and utilities
What features should I look for in a CMMS?
Consider these capabilities when selecting the right computerized maintenance management system:
- Work order management and scheduling
- Asset tracking
- Parts inventory management
- Mobile CMMS app
- Built-in barcode generator and scanning
- Audit capabilities
- Comprehensive records and reports
- Real-time notifications
- Customizable fields and workflows
- Multi-tenancy capabilities to track various locations
What are the benefits of a CMMS with built-in barcode technology?
Built-in barcode technology allows you to generate and print unique barcodes or QR codes for your assets and parts inventory. Using your CMMS mobile app, you can scan these asset tags with your phone's camera to quickly find or update records. A CMMS with built-in barcode technology helps your team improve data accuracy and save time.
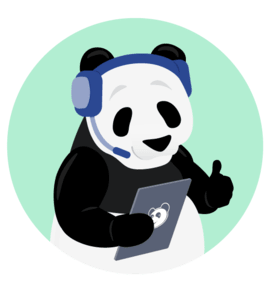
Learn more from an Asset Panda expert
Get a FREE consultation with an asset tracking expert to find out how you can transform your asset tracking.
Contact our Sales Team at (888) 928-6112